Direct Alpine s.r.o. is primarily a manufacturer of high-quality technical outdoor equipment. To achieve this level of quality, it is essential not only to use high-quality materials, precisely crafted patterns, and designs but also to incorporate modern technologies that significantly aid production and ensure the perfect quality and appearance of individual details, including the high-performance parameters required (waterproofness, breathability, wind resistance, and many others).
The most commonly used technologies in the production of outdoor clothing include seam taping, welding, laser cutting, and more. Some of these technologies are also applied to our products, and we will briefly explain them below.
Seam Taping
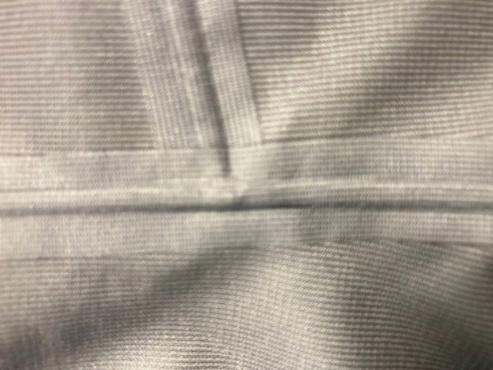
Seam taping is primarily used in hardshell clothing to prevent moisture from penetrating through the seams into the inner layers, keeping the user dry. Seams can either be taped with special adhesive tape – as seen in products such as Comet, Deamon, Talung, Guide, Midi – or covered from above with tape. The second method is often referred to as "welding" (tape welding or sealing). Nowadays, it is also possible to tape softshell materials, but before applying the adhesive tape, the seam area must be smoothed, or "sanded," to create an even surface. For a perfect finish on the reverse side of the product, you can select tape with the same pattern as the underside of the outer material, ensuring that our products look flawless and meticulously crafted, even on the inside.
The taping process itself is carried out on specialized machines where the sewn seam is fed through taping rollers along with the adhesive tape, and pressure and heat are used to firmly bond the tape to the seam. Throughout the process, it is important to ensure the correct parameters are set, and the operator of the taping machine must be skilled. The result is completely waterproof seams and a perfect appearance even on the inside of the product. The image below shows a detailed view of the tape application process.
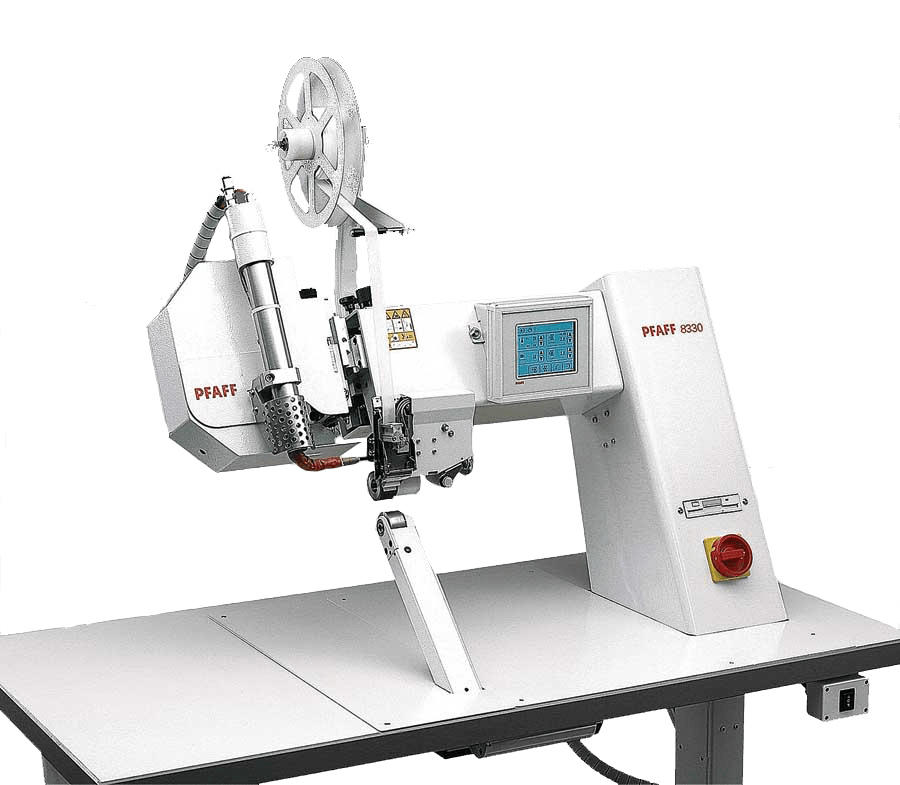
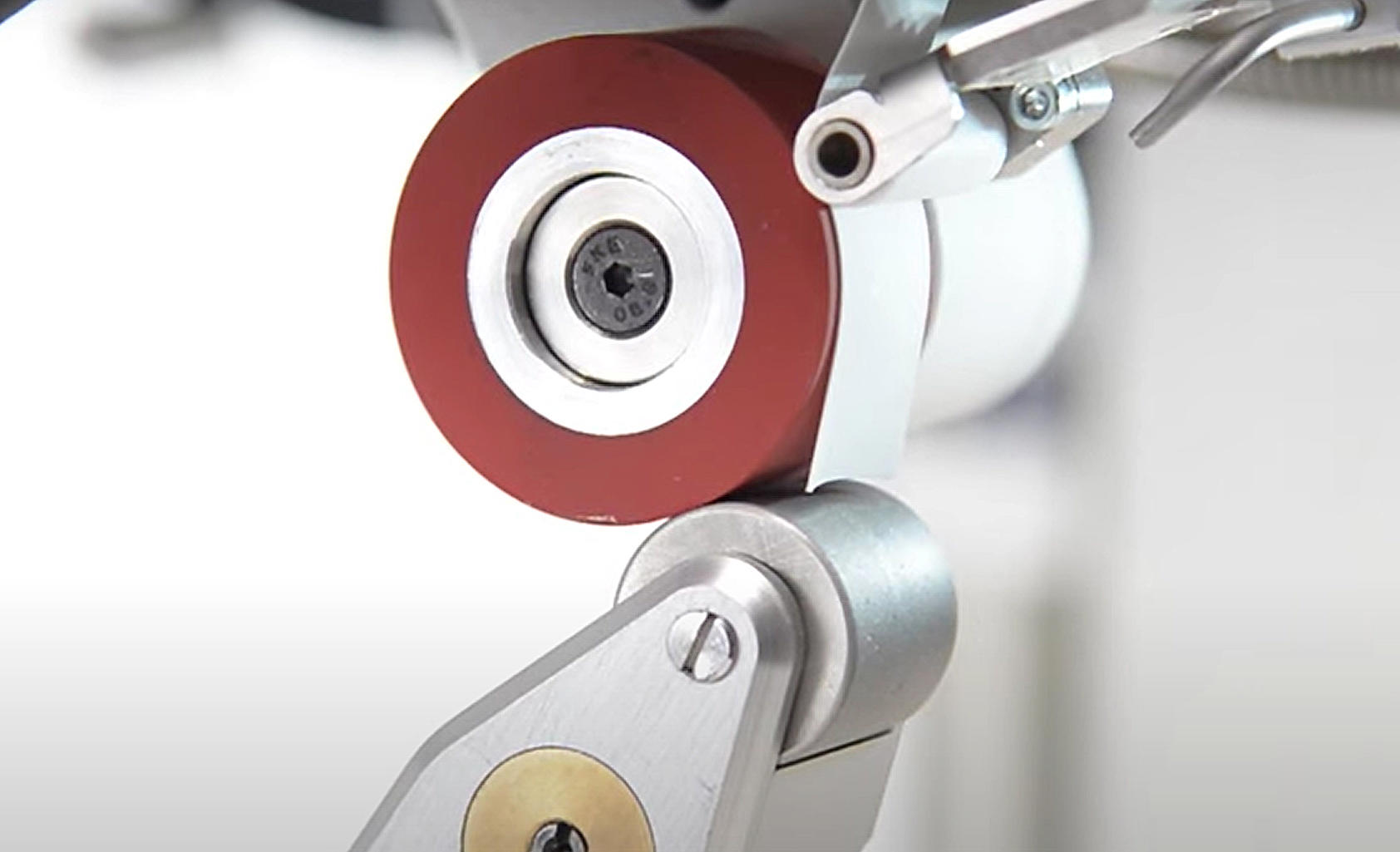
On some of our products, we also use a combination of several technologies, where we cut out desired shapes using a laser and then "press" them onto the finished product using heat and pressure. This method can be used to insert pockets into pocket openings, ensuring 100% waterproofing, or to seal certain seams or create eyelets for hood adjustments.
Laser Technology
Laser technology is most commonly used for cutting small parts or additional components, such as hood facings, toggles, Velcro, pocket openings, and much more. The main advantage is that it seals the cut edge, preventing the material from fraying, making it easy to sew or bond to the finished product. Laser cutting can also be used to create small openings that serve as ventilation under the arms, on the back, or as breathing holes on the Guide jacket.
Another technology involves reinforcing individual parts by applying special adhesive film. This is mainly used for visors, where it is important for the visors to hold their shape perfectly, or for reinforcing toggles or zip garages.
Design Highlights
All our products are developed in-house in Kateřinky, Liberec, and every jacket, pair of pants, or sweatshirt undergoes a meticulous design and construction process. All patterns are created using software tailored to the exact dimensions of individual sizes. This specialized software also allows us to create custom patterns or develop atypical sizes. We pay close attention to the ergonomics of the cut, ensuring that our clothing fits perfectly and does not restrict movement. All our products are then tested in the field, and based on feedback from our ambassadors, the designs are further refined as needed.
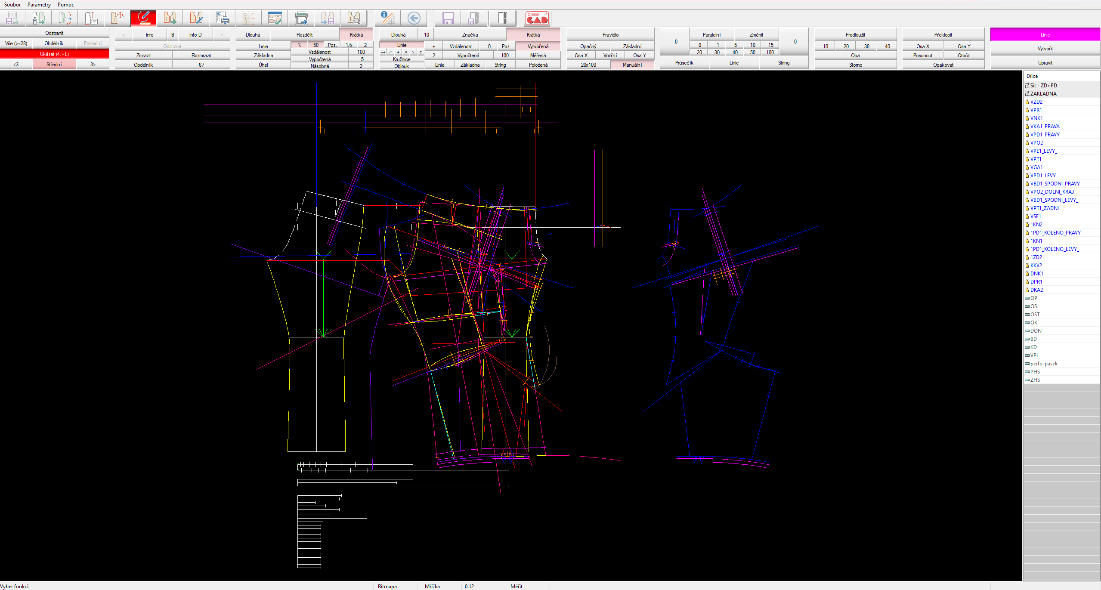
Hybrid System
The purpose of the Hybrid System is to utilize the specific properties of different materials and position them correctly on the product. For example, we consider the placement of sweat zones on the user’s body, wearing a backpack that may damage certain materials, and other factors. In the shoulder area, it is advisable to use more durable materials, while in the armpit area, more breathable materials are preferable. For better functionality, various perforated materials or functional knits are often used.